Maximaal productieresultaat dankzij Design for eXcellence
Design for eXcellence (DfX) levert grote meerwaarde op voor opdrachtgevers. Bij VDL TBP Electronics is deze aanpak opgenomen in de early supplier involvement. Door in een vroeg stadium invloed te hebben op het ontwerp van een printed circuit board assembly (pcba) realiseert de onderneming de hoogste productkwaliteit en productbetrouwbaarheid, volledig maatwerk, maximale leveringsflexibiliteit en de laagste totale kosten. De beste resultaten worden bereikt als opdrachtgevers alle fases benutten.
‘Het herstellen van fouten brengt kosten met zich mee die elke volgende processtap met een factor tien toenemen’, legt Steven Van Hout van VDL TBP Electronics uit. Hij is Manager Test Engineering & Electronics Test Development. ‘Ook kunnen fouten de kwaliteit (levensduur) van het product beïnvloeden. Door al in de ontwerpfase onze productiekennis en -ervaring in te brengen, voorkomen we dergelijke hoge kosten en bereiken we een zeer hoge uitleverkwaliteit. Liever vóórdenken dan nadenken is ons uitgangspunt, zodat wij alles in één keer goed kunnen doen en uitsluitend datgene doen wat nodig is. ‘Right first time’ noemen wij deze doelstelling die we met Design for eXcellence (DfX) bereiken, als onderdeel van onze early involvement services.’
Right first time: uitsluitend de juiste dingen doen, in één keer goed
DfX-fases
Design for eXcellence bestaat uit opeenvolgende fases waarbij de specialisten van VDL TBP Electronics het ontwerp van de opdrachtgever vanuit verschillende invalshoeken beoordelen en aanbevelingen doen voor verbetering. Van Hout: ‘Het maximale productieresultaat wordt bereikt als fase 0 tot en met 2 volledig worden doorlopen. We kunnen ons productieproces dan optimaal inrichten, met grote meerwaarde voor de opdrachtgever.’
In de belangrijkste fase, namelijk fase 0, selecteert de ontwerper de keycomponenten. ‘Wij adviseren zoveel mogelijk categorie A-componenten toe te passen’, vervolgt Van Hout. ‘Deze zijn altijd op voorraad onder geconditioneerde omstandigheden en we beschikken over alle productie- en testgegevens. Wij dragen de verantwoordelijkheid voor minimale besteleenheden, de opdrachtgever neemt uitsluitend de aantallen af die hij nodig heeft. Voor specifieke opdrachtgevers hebben wij ook categorie B en C op voorraad. We adviseren de ontwerpers van onze opdrachtgevers en onze ontwerppartners niet alleen over de keycomponenten, we maken hen ook meer bewust van de testbaarheid, maakbaarheid en leverbetrouwbaarheid.’
Deze bewustwording vindt plaats in fase 1 dankzij de analyses Design for Testing (DfT), Design for Manufacturing (DfM) en Design for Logistics (DfL). Het specialistisch en ervaren engineeringsteam van VDL TBP Electronics ontwikkelt innovatieve toepassingen voor met name DfT en DfM, waaronder de efficiënte en effectieve extended boundary scan test (mixed signal test).
Design for Testing (DfT)
‘Het elektrische schema dat de ontwerper in dit stadium aan ons voorlegt, analyseren wij op testbaarheid en testtoegankelijkheid', legt Van Hout uit. 'De belangrijkste testmethode is onze Extended Boundary Scan (EBST) waarmee wij de pcba’s op productieniveau geautomatiseerd functioneel testen en zo de werking van de keycomponenten valideren. Het grote voordeel hiervan is het geautomatiseerd zoeken naar fouten en het aanmaken van een herstelticket. Door testpunten op te nemen in het ontwerp, kunnen we de extended boundary scan optimaal inzetten. Indien er sprake is van onvoldoende testtoegankelijkheid, kunnen wij toch een maximale testdekking behalen met deze methode door gebruik te maken van software van de opdrachtgever.’
De Extended Boundary Scan voorkomt kostbare functionele testoplossingen bij de opdrachtgever en beïnvloedt het productierendement en de productkwaliteit positief, uitgedrukt in ‘production yield’ (of ‘first pass yield’) en ‘slip through’. Van Hout: ‘Wij berekenen deze voorlopige percentages op basis van de complexiteit van het ontwerp en de toegepaste teststrategie, en nemen deze op in onze rapportages en offertes naar de opdrachtgever. Ontwerpers beoordelen met name de functionaliteit van het ontwerp, wij denken mee over de testbaarheid en testtoegankelijkheid. Zonder overigens de economische kant uit het oog te verliezen. Dit doen wij door de testpunten zo efficiënt mogelijk in het ontwerp te verwerken.’
Design for Manufacturing (DfM)
In fase 1 onderzoekt VDL TBP Electronics ook de maakbaarheid van het ontwerp. Geert Gielis, DfM-engineer: ‘We controleren of de footprints op de pcb overeenkomen met de fysieke componenten en controleren met het softwaremodel of we alle componenten betrouwbaar kunnen plaatsen en solderen. Ons doel is om dit automatisch te doen en daarom komt een pcba met alleen maar smd-componenten het best in aanmerking. Vanuit ontwerptechnisch standpunt kiest de ontwerper soms echter voor conventionele componenten (through hole-componenten). Door in dit geval deels Pin In Paste (PIP)-varianten te selecteren, zijn ze toch door een pick & place-machine te plaatsen en zijn ze geschikt voor een hogere oventemperatuur (full reflow). Belangrijk is dat de overige conventionele componenten automatisch te solderen zijn (selective wave). Het handmatige alternatief, uitgevoerd door mensen, brengt meer fouten en meer kosten met zich mee, hoe zorgvuldig ze hun werk ook doen. Voor een geautomatiseerd ‘selective wave’-proces is ruimte tussen de componenten aan de soldeerzijde een vereiste. Hierop analyseren wij het ontwerp en onze aanbevelingen koppelen we naar de ontwerper terug.’
‘De praktijk heeft ons geleerd dat we in deze fase vrijwel alle productie-inefficiënties in het ontwerp ontdekken’, vervolgt Gielis. ‘Het komt bijvoorbeeld voor dat er enkele verkeerde componenten uit de stuklijst zijn geselecteerd. Dit is een administratieve fout die in deze fase nog relatief eenvoudig oplosbaar is. Hoe anders is het als we de hele productielijn al hebben ingesteld en de verkeerde componenten worden geleverd! Dan kun je helemaal opnieuw beginnen met alle kosten van dien. Het voorkomen van fouten voorkomt hoge kosten.’
Design for Logistics (DfL)
In de strategie van Design for eXcellence speelt ook de samenwerking met leveranciers een belangrijke rol. Belangrijke prestatie-indicatoren zijn kwaliteit, logistiek, technologie, kosten, communicatie en risicomanagement. Dankzij intensieve samenwerking en grote bestelvolumes kunnen voorkeursleveranciers hun tarieven voor de categorie A-componenten laag houden. Zij zorgen bovendien voor betrouwbare levering, ook van de minder toegepaste B- en C-componenten op basis van verwachte orders. De early involvement services van VDL TBP Electronics scheppen hiervoor de voorwaarden.
Design for eXcellence (DfX)
‘In fase 2 bereiken we het Design for eXcellence en controleren we zorgvuldig de maakbaarheid en testbaarheid van de hele pcba’, vervolgt Van Hout. ‘De definitief berekende percentages voor productierendement (production yield) en productkwaliteit (slip through) nemen wij als resultaatverplichtingen in onze offertes op en daarin zijn wij als EMS-onderneming uniek. Deze berekeningen hebben nog steeds betrekking op de ontwerpfase.’
Na goedkeuring ontwerp worden alle uitgewerkte processtappen in het productiebeheerssysteem opgenomen. Dit systeem bewaakt of alle stappen daadwerkelijk worden gezet en vergelijkt de berekende en gemeten production yield- en slip through-percentages. Indien nodig worden direct corrigerende maatregelen genomen. Het uiteindelijke resultaat is een pcba met de hoogste productkwaliteit en productbetrouwbaarheid, volledig op maat, met maximale leveringsflexibiliteit en de laagste totale kosten.
Right first time
‘Wij helpen de ontwerper direct de beste componenten, de juiste productiestappen en de beste teststrategie te kiezen voor het hoogst haalbare productieresultaat’, besluit Van Hout. ‘Dankzij onze early involvement services kunnen wij onze strategie van Design for eXcellence volledig toepassen. Natuurlijk kunnen we de pcba’s volledig volgens de specificaties van de opdrachtgever maken, maar dit levert niet het optimale eindresultaat op dat wij met onze aanpak van Design for eXcellence wél kunnen bereiken. Wij vinden de communicatie met de opdrachtgever en de ontwerpers in een vroegtijdig stadium erg belangrijk, zodat wij onze bevindingen kunnen toelichten. Hierdoor ontstaat wederzijds begrip en wederzijdse erkenning. Het bewustzijn groeit en dit heeft veel toegevoegde waarde. De effecten zien wij bij vervolgopdrachten, waarbij de ontwerpers steeds meer rekening houden met alle relevante aspecten. Liever vóórdenken dan nadenken en alles in één keer goed. ‘Right first time’ dankzij Design for eXcellence!‘
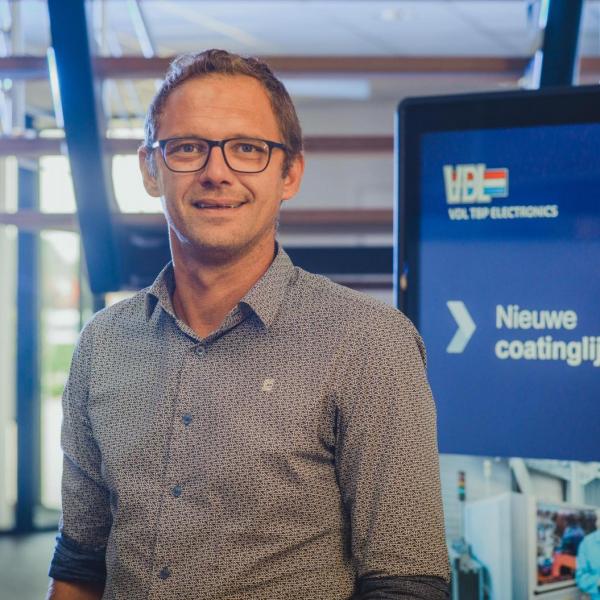